Supply Chain & Third-Party Vendor Resilience
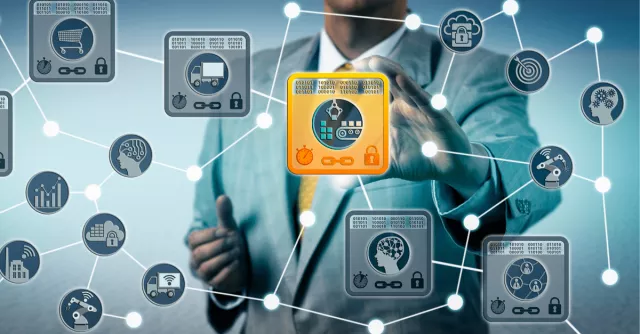
Our recent report in collaboration with The Conference Board, delves into some of the top trends in the business continuity landscape. Supply chain and vendor management has become a critical component in operational resilience as many organizations depend on critical vendors to perform or support crucial operations. A disruption in the delivery of those services can directly impact a company's resilience and, on average, costs a large company $184 million a year. Supply chain disruptions also hurt companies' reputations; 83% of companies reported that their firms have suffered reputational damage after a disruption.
President Biden recently issued an executive order designed to strengthen the resilience of America’s supply chain.
While the order directs some federal agencies to review existing supply chains and make recommendations to resolve current and future issues, it reinforces the importance for all organizations to take a proactive, end-to-end approach to supply chain resilience requiring optimization along all touchpoints of the supplier-to-customer route.
Added Focus on Vendors’ BC Plans
Organizations are performing greater due diligence on suppliers’ BC arrangements – according to the BCI Supply Chain Resilience Report 2021, 75% of organizations are ensuring their key suppliers have plans in place. During 2020, organizations performed greater levels of due diligence at the procurement stage of supplier relationships, with 38% now reporting BC checks are an integral part of the procurement process.
Though this trend was already beginning, the pandemic had a significant impact. Forty-nine percent of respondents reported management is “much more committed” to managing supply chain risk as a result of COVID-19. And according to Capgemini's Fast Forward report, more than 80% of organizations were negatively impacted by the pandemic, with major supply chain repercussions:
- 74% faced a shortage of critical parts or materials
- 74% saw delayed shipments and longer lead times
- 69% faced difficulties in supply planning due to a lack of information from their suppliers
- 69% had trouble quickly scaling production up and down
After these significant disruptions, 55% of organizations report taking three to six months to recover, with 13% expecting recovery to take six to 12 months. These are strong signals to companies of any size and industry to reexamine relationships with suppliers and ways to build resilience within supply chains.
Ways to Increase Supply Chain Resilience
Although companies must be mindful of budgets, certain changes in operations can help to increase supply chain resilience without adding significant costs, depending on the industry. Here are just a few:
- Reevaluate sourcing and shift from "just-in-time" sourcing
- Build redundancy
- Shift to direct-to-consumer marketing to meet customer demand
- Create new revenue sources
- Increase visibility across the entire supply chain
- Shift to ecommerce
- Diversify your supply chain
- Create plans that take into account a range of possible disruptions, including:
- Pandemics
- Environmental change or natural disasters
- Civil unrest
- Regulatory changes
- Fraud
- Theft
- Cyberattacks
- Evaluate and closely manage your vendors and suppliers (more on that below)
Best Practices to Help Regularly Assess Your Suppliers
1. Shortlist your top critical vendors.
Which vendors and suppliers does your company rely on most heavily? Those are the ones from who you should request business continuity documents in order to ensure that they, too, will maintain continuity in the face of disruption.
2. Engage with them and assess their susceptibility to multiple event scenarios.
These vendors should consider the same risks outlined in your organization's internal BCP(s). Ask vendors which types of disasters they've dealt with in the past and whether they recovered successfully. Just like your own company, these suppliers must have plans for many different types of unforeseen events.
3. Score your suppliers based on four essential elements.
Score suppliers based on planning (BCDR), physical recovery, approach to testing and exercising, and compliance with ISO 22302 standards.
4. Conduct scenario planning exercises and testing to ensure plans work as intended and recovery timelines are met.
Suppliers must be able to deploy their plans quickly in case of a disruption or disaster. Exercising and testing plans will help ensure that suppliers know their plans and are ready to execute them to maintain continuity. At Agility, we recommend making sure that your suppliers test their disaster recovery plans at least once a year. You can also invite suppliers to participate in your tests.
5. Regularly perform vendor due diligence.
Don't just check that vendors have everything in place when you first begin working together. Check in at least once a year to make sure that they are continuing to exercise, test, and adapt their plans based on changing threats and needs.
Read more about avoiding business disruption with supply chain resilience and maintaining operations.