Supply Chain Disruptions: Mitigating Risk Through Planning
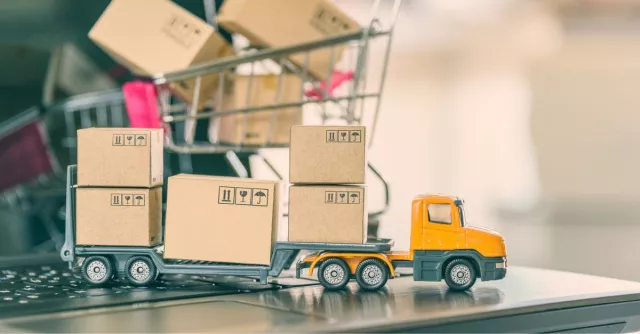
Supply Chain Disruptions and Their Impact
Supply chain disruptions can come from many places, and their impact is often far-reaching and complex. One of the most notable recent examples is the COVID-19 pandemic.
Retail sales and other in-person experiences plummeted amid early lockdowns, leaving businesses with billions of dollars in unsold goods that they purged with dramatic sales. However, as they got rid of this inventory, many manufacturers remained at limited capacity. Companies faced substantial shortages when the economy picked up again. Many supply chains are still trying to catch up to the ensuing backlogs.
Similar effects can arise from natural disasters. An earthquake or other event could shut down a factory and limit stock, leading to considerable backlogs and higher prices. Significant shifts in consumer trends can worsen things, creating a bullwhip effect if you over-adjust for goods that fall out of fashion or shortages for the opposite.
Geopolitical tensions and sanctions have also caused supply chain disruptions recently. The U.S. has imposed strict sanctions on Russian economic relations amid the Ukraine conflict, meaning some companies have to reevaluate where they source some goods or materials.
Restrictions against nations you have even a minor dependency on could cause significant problems down the line. You’d have to switch suppliers or risk hefty fines and that disruption could cause delays and stock shortages, leading to lost customers and missed sales.
How to Mitigate Supply Chain Disruptions
These disruptions have extensive consequences, so ensuring supply chain resilience is critical to incident management. It’s important to prepare for these incidents instead of assuming they’ll never happen. They can arise from anywhere and come with little to no warning, as the Ukraine conflict and COVID-19 highlight, so some disruption is inevitable. Here’s how you can mitigate the effects.
1. Maximize Supply Chain Visibility
You can mitigate supply chain disruptions more effectively if you respond quickly. That means being able to see potential issues as they arise, which requires visibility. Consequently, the first step in making a more resilient supply chain is gathering more data and keeping this information in an accessible, easy-to-use platform.
Internet of Things (IoT) tracking solutions can provide real-time updates on shipment locations and quality, which helps gain more insight into potential delays. You should also communicate more closely with suppliers and logistics providers to better understand issues that could affect you. A comprehensive data backup and recovery system is also a good idea, as maximizing visibility will leave you with more sensitive information.
2. Enable Flexibility
Next, you need to ensure your supply chain is flexible to allow you to adjust quickly to incoming changes. One of the most common issues to overcome is single sourcing. Many companies use one company for some products or materials, making it difficult to recover if something happens to the single source.
Find multiple suppliers, including some in nearby areas, to avoid getting stuck. You may also need to keep larger safety stocks of mission-critical items and materials.
Because supply chains are so interconnected, your partners and vendors also must be flexible. Be sure to evaluate vendors’ business continuity plans and frequently communicate with them to ensure everyone can adjust quickly if necessary.
3. Understand Your Risk Landscape
You’ll need a thorough understanding of the risks you face if you want to mitigate supply chain disruption as much as possible. You may not be able to prepare for every eventuality, but you can see what’s most likely or most damaging and focus on those.
Conduct a business impact analysis (BIA) to see what your supply chain is most vulnerable to and how those events would affect you. Once you understand these risks, you can form more effective backup plans and see where you can reorganize your supply chain to minimize vulnerabilities.
4. Build Contingency Plans
Once you have a detailed BIA, you can form backup plans around it. If your supply chain is highly vulnerable to factory shutdowns, plan how to switch to getting more from other suppliers. Develop a reshoring or near-shoring plan if international conflicts or shipping rates are some of your highest risks.
Form several contingency plans to address your biggest threats. Remember to keep these detailed, including specific steps to take, communication protocols and an outline of everyone’s responsibilities. A continuity strategy suite like Preparis will ensure these plans are accessible and shareable.
5. Review Your Risks and Plans Regularly
Realize that your risk landscape will evolve as your supply chain and the factors that influence it do. Different risks may pose larger threats, and industry best practices may shift. Consequently, you should regularly review your BIA and continuity plans to ensure they’re still applicable.
Risk management will become a key success driver for more than 50% of organizations by 2025 as supply chains grow increasingly complex and risk factors rise. Companies that continually reevaluate and stress the importance of their disruption preparedness will set themselves apart.
Supply Chains Need Business Continuity Plans
Some disruption is inevitable in any business. However, you can minimize the impact if you approach these risks proactively and plan to adapt to emerging situations ahead of time. Capitalizing on risk management and business continuity tools for your supply chain could save you from considerable losses in the future.
Zac Amos is the Features Editor and a writer at ReHack, where he loves digging into business tech, cybersecurity, and anything else technology-related. You can find more of his work on Twitter or LinkedIn.